Four Shaft Waste RDF Shredder
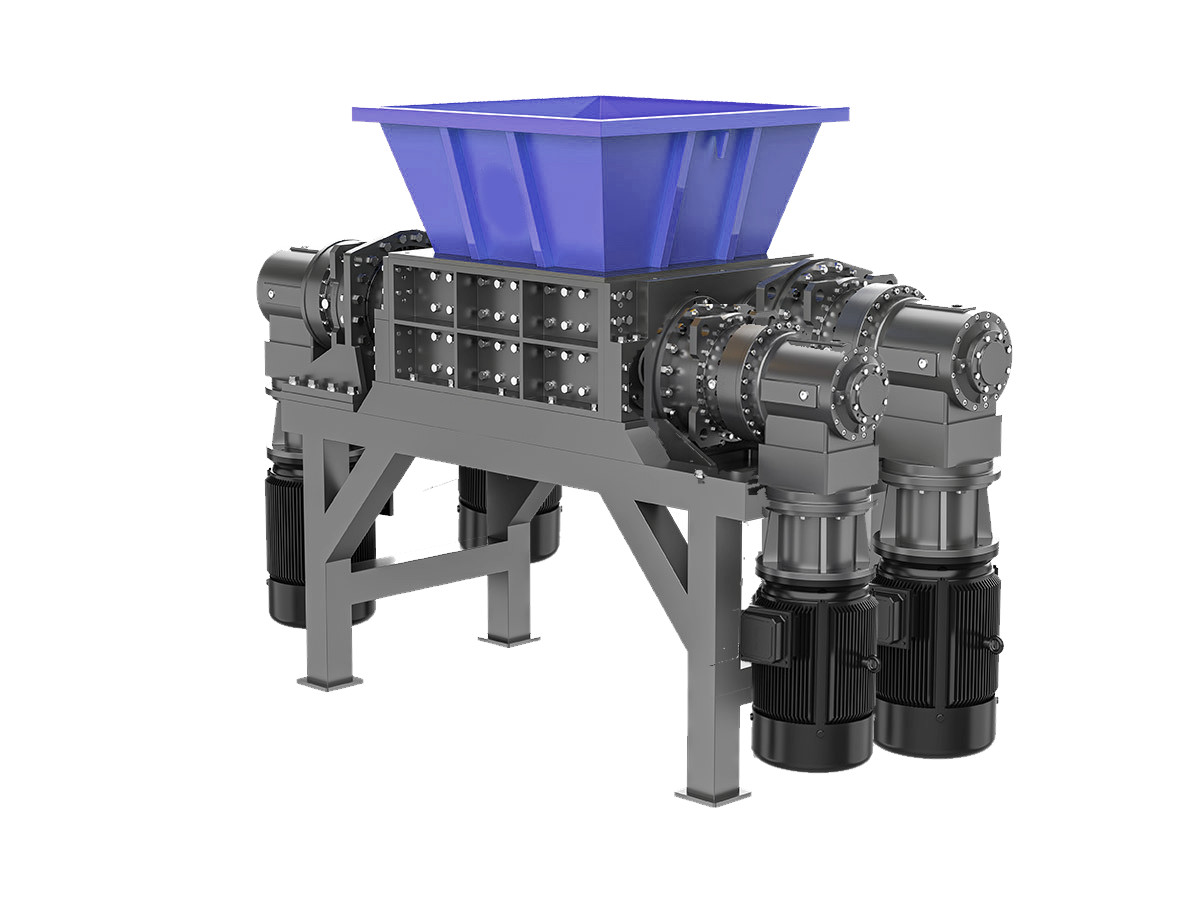
A four shaft RDF (Refuse Derived Fuel) shredder is an advanced industrial machine specifically designed for processing and shredding waste materials into fine, uniform pieces that can be used as alternative fuel in energy generation. RDF shredders are primarily used in waste-to-energy plants, recycling facilities, and waste management operations. The four shaft configuration, with two primary and two secondary shafts, ensures a high level of efficiency in breaking down a wide range of waste materials, including plastics, paper, rubber, textiles, and biomass.
RDF is created by converting non-recyclable waste into a fuel source that can be used in cement kilns, power plants, or other industrial furnaces. The role of a four shaft RDF shredder is to reduce large quantities of mixed waste materials into a consistent size that can be burned more efficiently, contributing to sustainable energy solutions. The robust, high-torque design of the four shaft shredder allows it to handle tough, mixed waste materials with ease.
With their superior shredding capabilities and high throughput, four shaft RDF shredders are integral to modern waste management practices, helping businesses and municipalities reduce waste volume while producing a valuable fuel product for energy generation.
Key Advantages of a Four Shaft Waste RDF Shredder
One of the key advantages of a four shaft RDF shredder is its ability to process a wide variety of waste materials into uniform pieces suitable for energy production. The dual-stage shredding system ensures that even tough materials such as rubber, plastics, and mixed waste can be reduced to the optimal size, improving the efficiency of the combustion process.
Another advantage is the high throughput capacity of four shaft shredders. The machine’s dual-stage cutting mechanism helps to achieve continuous material flow without clogging, allowing for large volumes of waste to be processed quickly and efficiently. This makes four shaft RDF shredders ideal for high-demand applications such as power generation and large-scale recycling plants.
Additionally, four shaft RDF shredders are designed for long-term durability and minimal maintenance. Their heavy-duty construction and wear-resistant cutting blades ensure a long service life, even when operating in harsh industrial environments. Many modern models also feature advanced control systems, including overload protection, reverse operation to prevent jamming, and adjustable shredding settings, allowing operators to customize the machine’s performance based on the waste material being processed.
How a Four Shaft Waste RDF Shredder Works
The shredding process in a four shaft RDF shredder begins when waste material is fed into the intake system. The two primary shafts, equipped with high-torque cutting blades, grip and tear the material into large fragments. These larger pieces are then fed to the secondary shafts, which further reduce them into smaller, uniform pieces suitable for energy production.
Unlike other shredding systems that rely on high-speed grinding, four shaft RDF shredders operate at a lower speed with higher torque. This design reduces the production of dust and minimizes the risk of overheating, ensuring efficient shredding with a higher degree of safety. The controlled, low-speed operation also helps preserve the integrity of the material, improving its combustion characteristics.
Modern four shaft RDF shredders come with intelligent control systems that monitor various aspects of the shredding process, such as load, speed, and output size. These systems help optimize machine performance while reducing energy consumption and wear. Features such as reverse rotation to clear blockages and programmable shredding settings for different types of waste further enhance the versatility and efficiency of the shredder. With their reliable and eco-friendly performance, four shaft RDF shredders play a vital role in modern waste-to-energy applications and sustainable waste management.